Chlor-Alkali Solutions

At a glance
thyssenkrupp nucera® has been active in the chlor-alkali sector throughout the world for more than 60 years and realized over 600 electrolysis projects worldwide. We have implemented projects from small facilities to huge chlor-alkali plants with capacities of over 800,000 mt/year of NaOH.
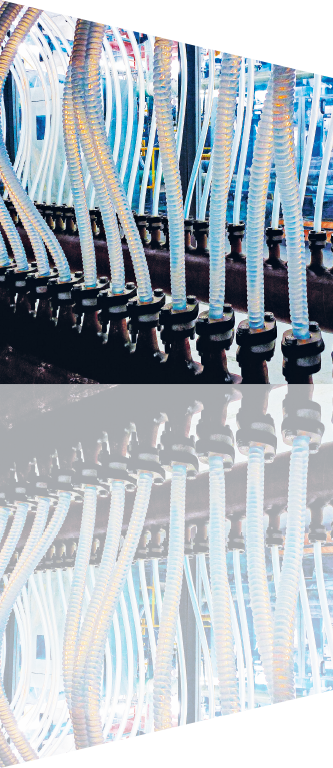
Bipolar membrane (BM) single element technology
Our bipolar membrane (BM) 2.7v6 plus single element offers optimized design features and thus breaks the barrier of 1,980 kWh per metric ton of NaOH at 6kA/m². Highlights are an accessible active area of 2.85m² and a longer membrane life under high current density operation beyond 6 kA/m².
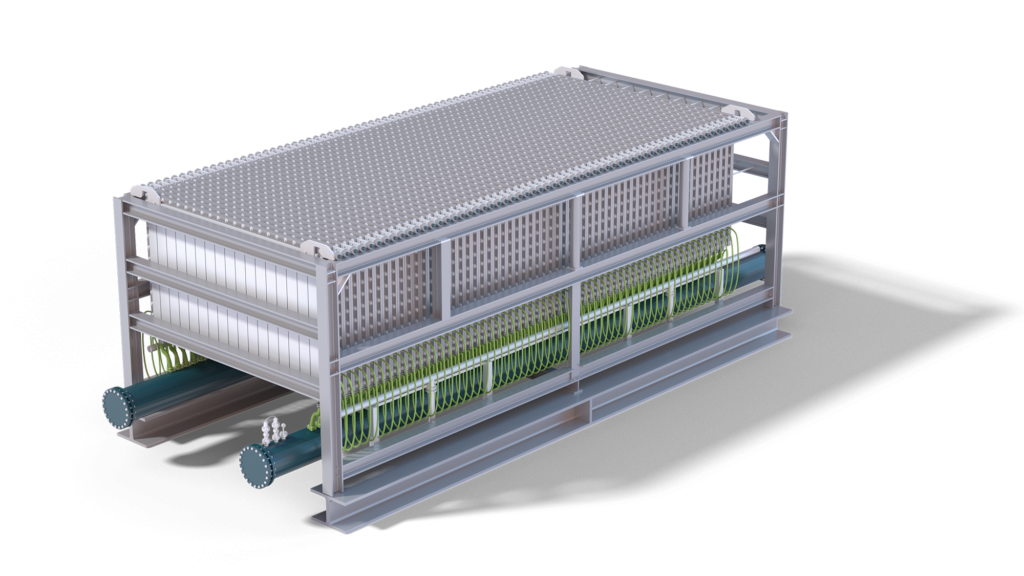
- Energy savings
- Enhanced energy efficiency
- No leaks
- Contact pressure independently controlled
- Extended membrane service life
- Unique sealing and hose system, 100% leakproof up to 4.7 barg (operating pressure: below 0.5 barg)
- Roller suspension of each single-element ensures precise adjustment of contact pressure
- Hard, long-wearing PTFE gaskets
- Assembly and testing of elements in clean area outside cell house
- Fast and simple replacement of elements with fully pre-tested elements
- Only one element type in one electrolyzer (no special end elements required)
- Power consumption: 1,980 kWh per metric ton of NaOH at 6 kA/m²
- Accessible active area: 2.85m²
The figures above are to be understood as ‘expected values’ and may vary depending on operating conditions.
Bipolar ion-exchange membrane process electrolyzer (BiTAC)Â Â
Our proven filter press bipolar ion-exchange membrane process electrolyzer, BiTAC®, offers specific advantages, such as fast remembraning of the complete electrolyzer. The BiTAC family is being constantly improved and all generations are compatible, so existing plants can easily be upgraded to the latest developments. The latest generation, eBiTAC-v7, pushes energy consumption to a new record low of 1,979 kWh/t NaOH at 6 kA/m².
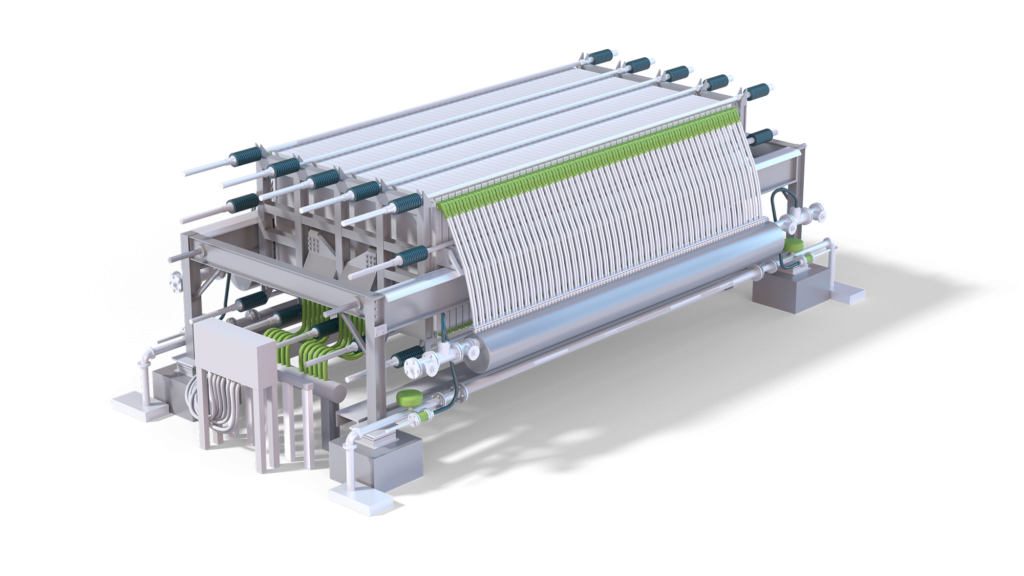
- Low sealing force required for gaskets, no bolts needed
- Fast remembraning of complete electrolyzer
- Smaller maintenance area required
- Lower power consumption through joining anode and cathode compartments by explosion bonding
- Fine anode mesh reduces cell voltage
- Smooth anode surface with no dents thanks to unique spot-welding tip
- Superior separation of gas and liquid
- Single piece of cathode mesh to fill gap losses and maximize active surface
- Elastic MWX spring with a large number of contact points to decrease IR drop and make homogeneous distribution of current density possible
- Superior inner circulation to ensure uniform concentration and brine supply
- Optimized current conductivity: 30,000 contact points per element
- Power consumption: 1,979 kWh/t at 6 kA/m²
- Operating temperature: up to 90 °C
- Product outcome: 32 % NaOH
The figures above are to be understood as ‘expected values’ and may vary depending on operating conditions.
Oxygen-depolarized cathode electrolysis technology (ODC)Â
Our NaCl-ODC (oxygen-depolarized cathodes) electrolysis technology is reliable and well-proven. It offers a higher degree of site flexibility with regard to electricity and hydrogen supplies.
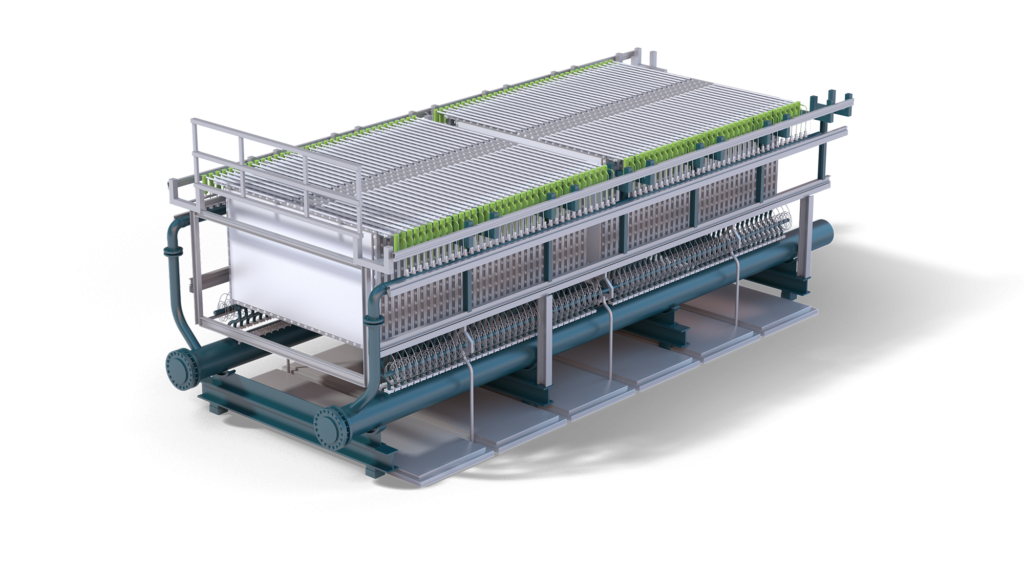
- Up to 25% reduction of energy consumption compared with conventional membrane-based technology
- Ecologically valuable solution due to corresponding CO2 emission reductions
- Higher site flexibilities regarding electricity and hydrogen supplies
- BM2.7 and ODC technologies combinable in a single plant thanks to full compatibility of electrolysis cells and brine cycle
- Roller suspension of each single-element ensures precise adjustment of contact pressure
- Hard, long-wearing PTFE gaskets
- Assembly and testing of elements in clean area outside cell house
- Assembled elements can be stored for many months
- Fast and simple replacement of elements with fully pre-tested elements
- Only one element type in one electrolyzer (no special end elements required)
- Power consumption: 1,550 kWh per metric ton of NaOH at 6 kA/m²
- Accessible active area: 2.72m²
The figures above are to be understood as ‘expected values’ and may vary depending on operating conditions.
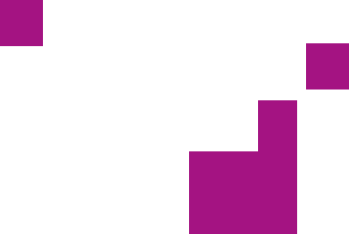
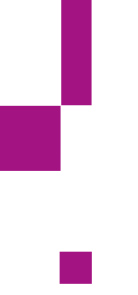
Integrated process solutionsÂ
At thyssenkrupp nucera we offer state-of-the-art products that feature engineering of the highest quality while taking economic, ecological and safety considerations into account. We offer solutions for the entire process, such as brine treatment, chlorine treatment, refrigerant free chlorine liquefaction or hypochlorite production.
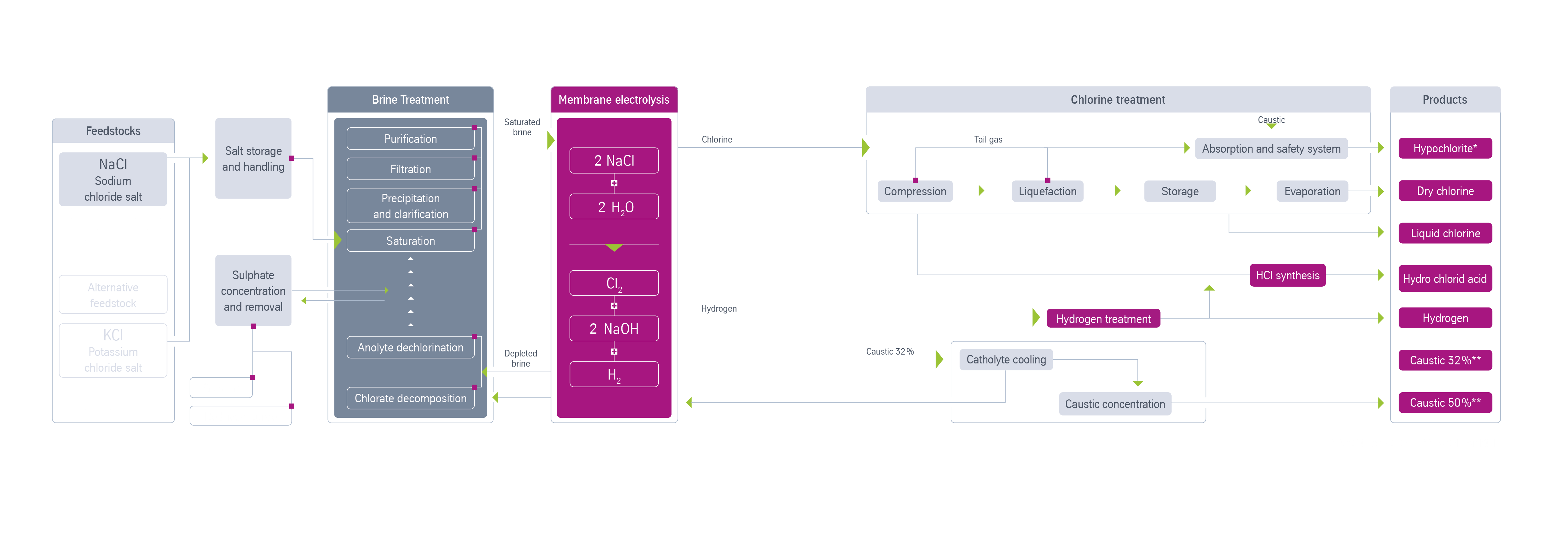
Brine Treatment
Efficient brine treatment protects the
membranes in the electrolysis cells while
at the same time keeping both investment
costs and operational costs to a minimum.
Chlorine Treatment
The chlorine generated leaves the cells with the
depleted brine. If high-purity chlorine is required
(e.g. for a downstream VCM plant), hydrochloric
acid can be added to the feed brine to reduce the
oxygen content in the chlorine produced.
Refrigerant free chlorine liquefaction
Chlorine from membrane electrolysis cells contains
some oxygen which might be required to be reduced
for specific downstream use. The liquefaction of the
compressed chlorine is performed in one or two stages
in heat exchangers (condensers).
Hypochlorite production (optional)
Sodium hypochlorite (bleach) is one of the
commercial chemicals typically produced by
our standard unit. It is at the basis of the water
disinfection and cleaning industries, and is
produced by direct reaction between the chlorine
and caustic soda resulting from the electrolysis
process.
Services along the product cycle
- Feasibility studies / technology selectionÂ
- Project management
- Arrangement of financing schemes
- Financial Guidance based on an intimate knowledge of local laws, regulations and tax procedures
- Environmental studies
- Licensing, incl. basic / detail engineering
- Utilities / offsites / infrastructure
- Procurement / inspection / transportation services
- Civil works and erection
- Commissioning
- Training of operating personnel
- Plant operation support / plant maintenance
- Full service
- Long-term partnership
- Spare parts supply & management
- Upgrade and retrofit
- Revamps
- Digital plant monitoring and optimization (web-based evaluator and remote condition monitoring)
- Consulting
- Service center & field services
Brine Treatment
Efficient brine treatment protects the membranes in the electrolysis cells while at the same time keeping both investment costs and operational costs to a minimum.
Â
Chlorine Treatment
The chlorine generated leaves the cells with the depleted brine. If high-purity chlorine is required (e.g. for a downstream VCM plant), hydrochloric acid can be added to the feed brine to reduce the oxygen content in the chlorine produced.
Â
Refrigerant free chlorine liquefaction
Chlorine from membrane electrolysis cells contains some oxygen which might be required to be reduced for specific downstream use. The liquefaction of the compressed chlorine is performed in one or two stages in heat exchangers (condensers).
Â
Hypochlorite production (optional)
Sodium hypochlorite (bleach) is one of the commercial chemicals typically produced by our standard unit. It is at the basis of the water disinfection and cleaning industries, and is produced by direct reaction between the chlorine and caustic soda resulting from the electrolysis process.
Execution concepts
Compact cell-house designÂ
This largely standardized design is optimized to deliver low total investment costs, minimize space requirements and ensure easy maintenance. The cell house has no pits and the catholyte system is an integrated part of the design.Â
Skid-mounted technologyÂ
Skid-mounted chlorine plants have a capacity of 5,000 or 15,000 mt/a of Cl2Â and consist of standardized, pre-assembled modules in steel skids. Benefits: Lower cost, fewer civil and erection works on site and much faster project schedule than conventional plants. Â
Making a difference – together
We can only do pioneering work if we leave the usual business behind. If we show promise to the future generations. If we deliver. We can only deliver and achieve our goal if we work together. That’s why we collaborate with strong partners on the road to decarbonizing industry.
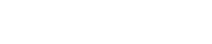
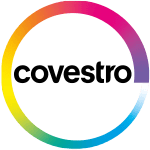

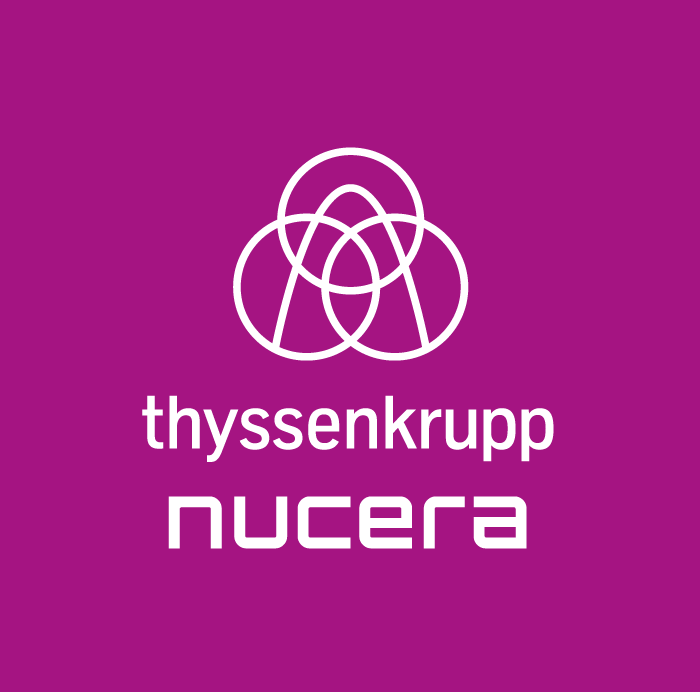